
-800x600-bed.jpg)

And even more importantly, it enabled us to define, in the design phase, the permitted costs of the solution and its performance in the part program. This standard made it possible, for the first time, to model the existing technology and to evaluate new ideas from our customers’ real production perspective. The result was a representative production program – the “original standard” by which we measured productivity, production problems and the impact of those problems. Customers from a variety of industries helped us with this by providing several hundred set-up plans, which we then analyzed statistically based on a variety of relevant parameters. To that end, we developed standard sheet layouts that model the range of parts our customers use. Riesenhuber: We had to make productivity measurable, and we had to do it using real parts under real production conditions. Riesenhuber: We also formulated clear efficiency and process reliability targets for the machine, and used these to assess each development stage. It was the first time we had applied agile methods across the board in a mechatronics project. The novel aspect was that all specialist departments worked in parallel and agreed on things among themselves in very short intervals. But to achieve overall success we needed lots more ideas, and these had to specifically tackle the problems we were facing. Of course, it was a brilliant idea that sparked this radical new development. In other words, you not only developed something new, but you did it in a new way?Įpperlein: Exactly. That’s why we fundamentally shifted our perspective – away from current machine design and toward an unobstructed view of our customers’ Peter Epperlein: We knew going into it that we would have to question existing development methods if we wanted to achieve a true leap in innovation with this mature technology.
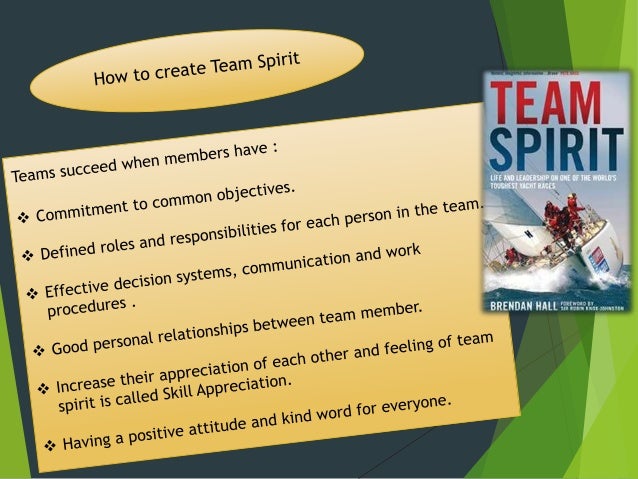
The initial idea for the TruLaser Center 7030 emerged in 2012, and the project was officially approved in 2014. How and when did the TruLaser Center 7030 project come about?įelix Riesenhuber: TRUMPF had long wanted to develop the next generation of laser-cutting machines. In an interview, they spoke with us about the highs and lows of the past few years and told us what it takes to develop such a novel product. Talking to someone in a certain field always adds to your understanding of the issue.Felix Riesenhuber, Peter Epperlein and Jens Ottnad were heavily involved in designing, developing and implementing the new TruLaser Center 7030. In my experience, you get many more responses than you would expect. What is your ultimate tip to other students?ĭon’t hesitate to approach people! I have learned so much by just trying to get in touch with businesses, academics or experts from various fields. You can follow my journey on my LinkedIn and, if you are interested in following my start-up, then make sure to check our Young Urban Engineers LinkedIn. We hope our start-up will give companies a fresh perspective on contemporary urban issues. Here we connect interdisciplinary teams of students to real-life projects, just like we ourselves experienced in the Urban Greenhouse Challenge. Together with two fellow team members, Hanna Winters and Titus Venverloo, I founded a start-up: Young Urban Engineers. This way of working is really something that I want to pursue. We surprised a lot of people - including ourselves - with the innovative and creative end result: “The Turtle”. I was team captain of TeAMSpirit, and it was so inspiring to see how an interdisciplinary team can actually bring out the best in one another. It was the perfect way to bring everything I’d learned so far a step further.
